第一章 绪论
1.1 研究背景
陶瓷装甲材料是目前应用最广泛的一种装甲材料。陶瓷装甲材料由陶瓷面板和背板材料组成[1-3]。陶瓷面板对装甲材料的安全性非常重要,它承受装甲材料的绝大部分伤害。虽然“脆”性严重影响了陶瓷在诸多领域的运用,但是除了脆性之外,陶瓷材料自身耐高温、高抗压、耐磨性等诸多性能非常优异,非其他材料可以替代,因此在高温、高外加压力的抗弹条件下,使用陶瓷作为防弹材料,可以充分发挥陶瓷的优异性能。本课题结合在实习工作时工厂实际开发研究项目,针对氧化铝陶瓷材料对其抗压性能及稳定性进行研究,探究高抗压强度和高稳定性的装甲陶瓷材料的制备工艺。
1.1.1 装甲车辆防弹材料的发展
随着各个国家在战略武器大规模发展的情况下,现代战争的对抗程度演变的越来越激烈,战场范围在现代先进的武器下变得越来越模糊,军用车辆及各类重要的武器设施受到各种武器的打击,破坏程度更加严重。为确保战争的胜利,对军用车辆、飞机和其他重要的军事设备及参战人员防护水平要求越来越高;眼下研究军用车辆等装甲防护技术,提高军用车辆等战场防护水平显得尤为迫切和重要[4-5]。
由于装甲材料用于装甲车辆、坦克、自行火炮、直升机以及单兵防弹服、头盔、防弹盾板等,装甲系统的轻量、高效对提高军机、坦克、装甲车辆以及作战人员的机动性、攻击力、战场生存能力来说至关重要[6]。从装甲材料的历史发展来看,从简单的金属材料到现在先进的复合材料(聚合物基、金属基)、陶瓷装甲材料,眼前的装甲材料应具备:高硬度、高强度、高韧性、低密度特点。纵观古今中外,用做装甲的材料大体有四类:金属、玻璃、Kvealr、陶瓷及其复合材料。
.................
1.2 国内外研究状况
1.2.1 装甲陶瓷安全性能国内外研究现状
李永东等对以 Al2O3陶瓷作面板、以石墨与超高分子量聚乙烯杂交纤维增强环氧树脂基复合材料为背板的复合装甲的抗弹性能进行了理论分析和实验研究,探讨了面板与背板的材料参数、几何参数等对复合装甲的抗弹性能的影响,得出双板复合装甲结构可以使面板和背板的力学性能得以扬长避短,实现良好匹配,达到提高综合抗弹能力的目的。
崔琳等对适合于作装甲的陶瓷材料的抗弹性能及价格进行了分析,并在此基础上选出了效-费比高的陶瓷装甲材料。通过陶瓷在装甲中的位置及用量对抗弹性能的影响分析,提出了具有最佳“效-费”比的复合装甲结构[29]。
孙素杰用 12.7 mm 穿甲弹对几种不同背板的陶瓷复合装甲进行了实弹射击实验,以研究复合装甲中陶瓷与背板组成的界面对其抗枪弹性能的影响。实验中在有效弹速下,以弹丸在后效板上的垂直残余穿深来作为衡量陶瓷复合装甲抗弹性能的指标。陶瓷复合装甲由 Al2O3陶瓷层和不同密度的均质材料组成。根据实验结果及对其的分析讨论,看出随着背板材料声阻抗的提高,界面阻止弹丸侵彻的能力也是降低的[30]。
陈智勇将陶瓷材料应用于防弹领域之中已成为近年来国内外研究的热点,陶瓷复合装甲的结构设计对防弹车辆的防护性能至关重要。从防弹车辆防护等级要求入手,以陶瓷/纤维复合装甲防弹机理为依据,从陶瓷面板、背板材料和约束形式三个方面出发,探讨陶瓷复合装甲防弹性能的主要影响因素。重点讨论陶瓷力学性能、尺寸、形状、厚度、背板及约束方式等要素对防弹性能的影响,寻求提高陶瓷复合装甲防弹性能的有效途径,为今后陶瓷复合装甲的结构设计提供理论基础和研究方向[31]。
.......................
第二章 试样制备及其性能表征方法
2.1 实验原料
原料是制备陶瓷的基础,原料的选择对于陶瓷材料的制备成功与否非常关键。种类、形貌、原晶尺寸等多个方面对材料性能有很大影响;原料种类则确定了材料的种类,种类不同,材料的性能不同;形貌对材料的性能也有较大的影响,片状形貌,晶粒在长大的过程中各方向能量不同,生长速度不同,造成晶粒生长不均,晶粒出现粗大现象,继而降低了材料的力学性能;原晶尺寸是制备微晶陶瓷甚至纳米陶瓷的先决条件,另外一方面原晶尺寸较细,粉体的活性较高,容易实现烧结,并且可得到晶粒较细小的陶瓷,这对陶瓷材料的性能有大幅度的提高。
本实验采用济南泉润科技有限公司 99 氧化铝造粒粉。表 2.1 和表 2.2 分别显示了原料的化学成分和粉料的粒度,由成分可看出,原料中氧化铝含量大于 99;从粒度分析可看出,D50 为 0.554um,D90 为 0.985um,粉料较细,如图 2.1 所示。
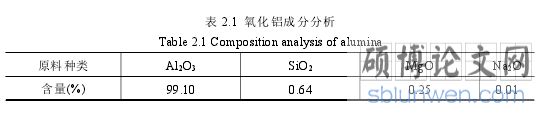
表 2.1 氧化铝成分分析
2.2 实验设备
实验设备是完成实验的工具,手动压机是完成干压成型的主要设备,根据设定的试样尺寸,选择模具,由模具的表面大小结合成型压力大小,确定施加的压力,当压力达到设定压力时,保压 10s 完成压制;箱式电阻炉主要是完成试样的烧结设备,按照设定的升温曲线,将试样放置在箱式电炉中,完成烧结;扫描电子显微镜是测试完成烧结试样的微观结构设备,可以直观观察到烧结完成试样的晶粒尺寸大小和结构均匀性;电子天平和液体静力天平分别对完成烧结试样的干重、湿重、浮重进行测量,利用阿基米德原理测量试样的气孔率、体积密度的设备;真空泵对试样干重、湿重、浮重进行辅助测量;电子万能实验机对试样的抗压强度进行测量;激光粒度仪对研磨粉料的粒度进行测量,控制粉料的尺寸大小;游标卡尺对试样收缩率进行测量,测量试样的尺寸。
实验具体所用主要实验设备如表 2.3 所示。
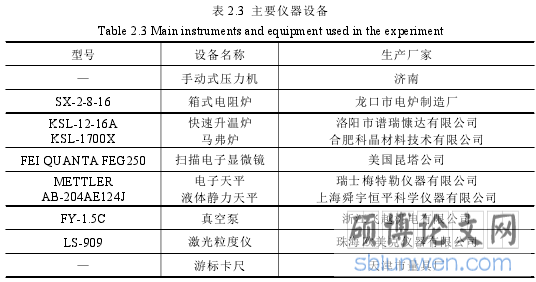
表 2.3 主要仪器设备
第三章 干压成型工艺对氧化铝陶瓷性能的影响................................24
3.1 线收缩率...............................24
3.2 显气孔率.......................................26
第四章 等静压成型工艺对氧化铝陶瓷性能的影响...............................41
4.1 线收缩率..........................41
4.2 显气孔率......................................42
第五章 结 论................................46
第四章 等静压成型工艺对氧化铝陶瓷性能的影响
4.1 线收缩率
等静压成型试样的线收缩率平均值如表 4.1、图 4.2 所示。
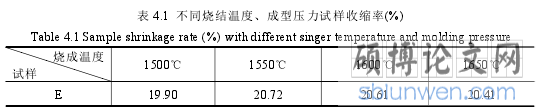
表 4.1 不同烧结温度、成型压力试样收缩率(%)
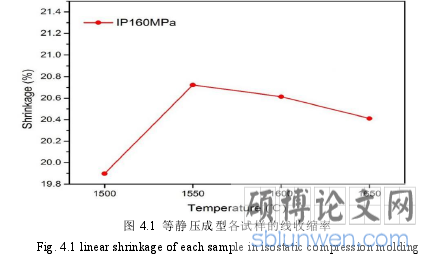
图 4.1 等静压成型各试样的线收缩率‘
.......................
第五章 结论
本论文主要结论是通过实验得出实际生产装甲车辆陶瓷面板的最佳工艺参数,首先使用干压成型制备 4 组不同成型压力的试样,再经过等静压成型制备一组试样,每组试样 40 个样本,设定四个不同温度点完成烧结,研究了烧结温度和成型压力以及等静压成型对氧化铝陶瓷的抗压性能和抗压可靠性的影响,同时对两种成型方式实验结果进行分析比较,得出如下结论:
(1) 成型压力对氧化铝陶瓷的抗压强度有较大的影响,干压成型方式下,随着成型压力增大,抗压强度增高,成型压力为 120MPa 所得性能较其他成型压力性能优良,抗压强度达到最高。weibull 模数与成型压力没有直接的线性关系,但在成型压力 120MPa,烧结温度 1600℃时,weibull 模数最大,此时稳定性最好。
(2) 两种成型方式下,烧结温度对氧化铝陶瓷抗压性能有明显的影响,随着烧结温度升高,等逐渐增大,当烧结温度为 1600℃,试样的最好。随着烧结温度升高,材料抗压强度与威布尔模数先增大后减小,当烧结温度为 1600℃时,各试样的抗压强度与威布尔模数均达到峰值,此时抗压性与稳定性最佳。
(3) 干压成型方式下,烧结温度为 1600℃、成型压力为 120MPa 时,试样的抗压强度最大,为 1073.75MPa,同时,Weibull 模数也达到最大值 7.676,即该条件下 99 氧化铝陶瓷兼得最大抗压强度和 Weibull 模数。
(4) 等静压成型可以有效地增加试样的气孔率、体积密度、收缩率等性能,但抗压性能低于干压成型方式。在等静压 160MPa 下,温度 1600℃时抗压强度最大,为 1062.59温度 1550℃时,Weibull 模数为 7.67,稳定性最好。但不能在同一温度下兼得抗压性能与稳定性能。
(5) 本文推荐在工厂实际生产装甲车辆陶瓷面板的最佳工艺参数是:采用干压成型,升温速率 2℃/min,成型压力为 120MPa,烧结温度为 1600℃,保温时长 2h。
参考文献(略)