第 1 章 绪论
1.1 课题的来源及研究意义
最近几年来,随着集成电路和微机电系统的推广,使得超精密微磨削技术也得到了快速的发展,对于结构比较复杂的三维微小零件的加工,更适宜用微型机床进行加工。国内外一些学者已经实现了应用微机械加工技术对多种材料进行加工,并且能够获得纳米级粗糙度的良好效果。数控技术是自动化制造技术发展的基础与关键,而数控编程技术却是数控技术发展的必要前提[1]。因此,数控编程技术在工业自动化发展中起到重要的作用。目前,在光纤端面加工过程中,光纤研磨抛光[2]主要是通过经验控制光纤与研磨砂纸之间的角度。光纤熔融拉锥[3]是通过控制拉锥时的温度以及拉锥时所施加的力的大小。光纤化学腐蚀[4]主要是通过腐蚀剂的浓度,腐蚀时间等。由此可见,传统的光纤加工技术存在过程比较复杂,生产效率低下等缺点[5]。同时,一般的微磨削加工通常采用手工编程方法,此种方法存在计算过程复杂、工作量大、编程时容易出错且效率极为低下,一组参数就要进行一次编程,对工艺操作人员要求比较高,不适合大批量生产[6]。针对目前所存在的问题,本文提出了基于PMAC可编程运动控制与VB6.0的结合,通过建立人机交互的模型,选择所要加工光纤的类型,然后填入该类光纤所对应的参数,就会自动生成系统能够识别的NC代码。这样在一定程度上降低了对操作人员的技术要求,提高了生产效率 ,具有重大的现实意义[7]。
...........
1.2 微型机床国内外发展现状及趋势
1970 年 dutta[8]等人提出微型机床进行切削加工的设想,启示了人类对微型机床的认识,该机床主要用于硅的微细削加工。在此之后,日本工业部也提出了微型制造系统。直到 1996 年日本研发了第一台微型车床[9],其结构如图 1.1 所示,才将这一设想变成现实。该台机床重量约为 100 克,车床总体尺寸为长 30mm 宽25mm 高 30.5mm,该机床的主要额定功率为 1KW。在加工直径为 60um 的黄铜棒时,其表面粗糙度大约为 1.5。切削功率远远小于普通车床。由此证明,微小型化的机床可以节省占地空间,提高资源的有效利用率。日本 Yoneyama 和 Lu[10]研制出了一台约 200mm 的微型铣床,该机床为三轴联动机床,其最小进给分辨率可以达到 4nm。主要参数为:额定功率 0.5KW,径向圆跳动为 1μm,电主轴的转速位于 3000-15000r/min 之间。在切削 0.3mm 的黄铜时,可以获得 1μm 的表面粗糙度。德国 WBK 大学成功的研制了亚微米精密铣床[11],该铣床的主要参数为:主轴最少分辨率可以达到 50nm,转速位于 1.6×105r/min 左右,如图 1.2 所示。之后,日本 M.Tanaka[12]等人研发了超精密微型车床的控制系统,可以加工直径为 0.9mm的球轴承。韩国首尔国立大学通过利用空气涡轮主轴,提高主轴转速,研制了一台五轴微铣床,该台铣床具有很好的加工性能[13]。邱时前[16]等人提出了基于工控机与 PMAC 运动控制卡组合的形式,成功的研制一台五坐标微铣削机床。该机床的定位精度可达 0.5μm,电主轴采用日本精工机械有限公司生产的 NSK E412 一 N41[17],其最高转速可以达到 40000r/min。哈尔滨工业大学精密工程研究所也已研制出了高精度的微型立式铣床,该铣床采用三轴联动,其机床设备如图 1.4 所示。
..........
第 2 章 基于 PMAC 的微磨床控制系统硬件的构建
2.1 微磨床结构介绍
本文主要利用自行研制的四轴联动微磨床,通过开发其专用控制系统,使其成为光纤端面加工的专用微磨床。其结构如下图 2.1 所示。该微磨床为四轴联动,分别由轴 1 控制机床的上下运动,轴 3 控制机床的左右运动,轴 2 控制机床的前后运动以及轴 4 控制光纤夹具的旋转运动。CCD 双目对位显微镜主要用于光纤在加工前的对刀,以及加工过程的检测。在加工光纤前,我们必须通过气压调整旋钮控制主轴的气压,当气压轴承表的指针正对 0.5 左右时,主轴才能够平稳旋转。此时,才能开启机床的主启动。超高速气浮主轴主要用于带动刀具高速旋转,其最高转速可以达 160000 转每分,我们可以通过气压表进行调节主轴气压,从而达到改变主轴的转速。光纤夹具主要用于夹持光纤,由于光纤直径非常小且属于脆性材料,因此不能直接用光纤夹具进行夹持,必须通过陶瓷插芯,从而起到保护光纤的作用。
........
2.2 微磨床控制系统硬件结构设计原则
本文主要通过工控机与 PMAC 可编程运动控制卡组合,搭建光纤端面微磨削控制系统。然而,在进行数控系统设计时必须遵循以下原则。(1)选择合适的总线标准。硬件的设计主要体现在总线的结构。开放式数控系统由各个模块通过总线进行相互联系和通讯。因此只有选择合适的总线标准,才能进行各个模块设计。然而模块的设计又可以分为实时模块和非实时模块两部分。实时控制模块在机床控制、数据采集、伺服驱动方面得到了广泛的应用。而非实时模块则是主要完成人机界面与 PMAC 的通讯,以及开放式数控系统的初始化,参数设计等一些基本功能。(2)层次化设计。所有的设计必须符合层次化设计标准,即以底层工控机 IPC为核心进行直接控制机床的运动。通过接线完成底层设备的控制与管理。利用PMAC 自带的 PLC 编程功能进行直接控制,从而提高系统的反应速度。(3)建立模块化标准。在进行数控系统设计时,模块化设计是非常必要。系统的模块化设计,可以使得系统简单易读,方便操作者操作。不仅如此,模块化设计可以反应出作者的设计思路,对于后期的系统维护非常方便。(4)系统的可靠性建立。对于新开发的数控系统,应该可以在不同的工作坏境下正常运转,即具有一定的可靠性。不能随着工作坏境的变化而发生变化,尤其在较为恶劣的工作坏境中。(5)能够进行二次开发。计算机领域的不断扩大,数控系统的开放性显得越来越重要。当加工零件发生变化时,我们可以进行简单的编辑,就可以实现数控系统的二次开发,这样使得数控系统得到了最大利用。
.........
第 3 章 基于 PMAC 零编程控制系统开发.....18
3.1 微磨床控制系统软件结构与功能分析 ........ 18
3.1.1 系统软件结构分析 .......... 18
3.1.2 系统软件功能分析 .......... 19
3.2 系统的软件设计过程 ...... 20
3.3 上下位机间的通讯 .......... 20
3.4 软件系统开发..........21
3.5 PLC 程序设计..........28
3.6 本章小结.......33
第 4 章 光纤端面加工精度的技术研究...........35
4.1 光纤端面加工存在的问题.........35
4.2 光纤端面加工零编程数学模型的建立.........36
4.3 光纤端面透镜微磨削加工角度试验研究.............39
4.3.1 试验装置与条件.....39
4.3.2 试验结果及分析.....40
4.4 本章小结.......45
第 5 章 光纤端面加工零编程系统的应用.......47
5.1 基于微磨床的光纤端面的加工过程.............47
5.2 基于零编程的光纤端面加工技术的应用.....51
5.3 本章小结.......55
第 5 章 光纤端面加工零编程系统的应用
5.1 基于微磨床的光纤端面的加工过程
光纤微磨削使用的一般方法是:1、根据要加工的光纤端面的形状以及精度要求选择合适的微磨棒;2、对选择好的光纤进行处理,使其变成裸光纤;3、将处理好的裸光纤插入陶瓷插芯上,并且用石蜡进行固定,装夹于夹具上;4 调整微磨床,并在自行开发的系统上填入微磨削参数;5、开始进行磨削,并通过 CCD 进行在线检测与观察;6、磨削完毕,光纤磨削成型。光纤磨削基本流程图如下 5.1所示:圆锥体光纤主要应用于光纤耦合以及光纤传感器领域,因此对于这种形状的光纤研究具有重大的现实意义。圆锥体光纤透镜主要是将裸光纤的端面磨削成几何圆锥形,通过电弧进行尖端处理,得到圆锥光纤透镜。因此,要制作出这样的圆锥体光纤透镜主要工作是磨削出理想的圆锥。圆锥光纤的磨削除了以上主要过程外还有自己特殊的步骤,具体步骤如下:1、利用剥皮刀去除光纤的包层,截取一段长度大约为 3 厘米的光纤。并且使用光纤切割刀进行光纤端面的处理。2、根据单模光纤的外径,合理的选择微磨棒。为了保证光纤端面微磨削能够获得较好的表面质量,根据脆性材料的去除机理,需要选择合适的磨粒直径。3、由于光纤的直接非常小,且属于脆性材料,用一般的夹具进行装夹显得非常困难,且光纤在加工过程中极易发生变形或者断裂。因此本文将裸光纤穿过陶瓷插芯进行装夹,并且用石蜡进行固定,防止在切削力的作用下,光纤与陶瓷插芯产生相对运动。待石蜡凝固后作为一个整体直接装夹与光纤夹具中,漏出 1.5 厘米长的裸光纤。4、先根据要求,设计好磨削圆锥体光纤的各种参数,如圆锥体的锥角、进给速度、主轴转速、磨削深度等。5、打开控制系统,在相应的系统界面上设置相应的参数。打开空气泵,调整轴承气压,使其必须固定在 0.5MPa,以免对主轴造成伤害。6、启动机床,光纤夹具旋转,通过调用程序进行对刀和磨削加工。7、磨削过程中,将光纤端面通过 CCD 监视器来观察和监测端面的磨削情况。以免进给量过大,造成光纤弯曲过大,或者折断光纤。磨削完成后,选择磨粒更小的微磨棒再进行磨削一次,以提高磨削后的表面质量。8、机床各坐标轴回零,利用 CCD 图像仪查看研磨的深度以及磨削的质量, 并检查光纤是否偏心。
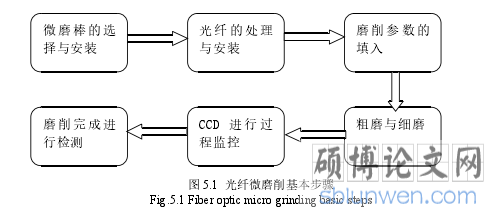
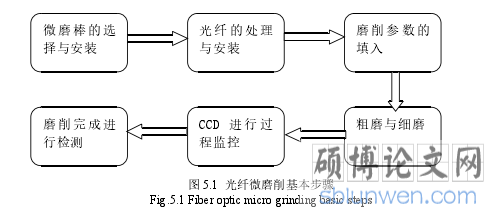
...........
结 论
针对传统光纤加工的不足和存在的问题,本文提出了基于光纤端面透镜微磨床专用控制系统零编程技术的研究,通过利用工控机和 PMAC 可编程运动控制卡的方法,有效的解决了目前所存在的问题。本课题在进行了大量的文献阅读和研究的基础上,得出了以下结论:(1)通过大量的文献阅读,了解到目前社会人们对光纤的需求量,以及光纤传感器和光纤之间的耦合效率对光纤端面形状精度的需求。本文提出了光纤端面透镜零编程控制系统的关键技术研究具有重大的现实意义。(2)根据学校已有的超精密微磨设备和可编程运动控制卡,为光纤端面透镜零编程控制系统的开发提供了硬件设备。通过分析光纤端面透镜零编程控制系统框架,功能模块,系统工作流程为光纤端面透镜加工零编程技术提供了可行性。(3)利用工控机和 PMAC 可编程运动控制器,进行微磨床控制系统的软件开发。主要包括软件的总体设计、上下位机的通讯、以及软件开发。其中软件开发包括工艺参数界面的设计、对刀界面的设计、手动模式的设计等。通过对这些功能界面的设计,完成了整个微磨床控制系统的开发。(4)对光纤在加工过程中角度变形与主轴转速,悬伸长度,进给速度之间的关系进行了试验与研究。通过实验所获得的参数进行分析和总结,并将所获得的规律以 PMAC 变量的形式作用于以开发的微磨床控制系统,从而使得加工精度在一定范围了得到了提高。(5)通过自行设计的微磨床控制系统进行加工光纤,以斜面光纤加工过程为例进行了详细的说明。从而验证了基于光纤端面透镜微磨床控制系统的可行性。除此之外,本文还加工了楔形 45 度光纤、锥形 30 度光纤。通过检测,其加工角度误差在 1 度之内,表面粗糙度在 374nm 左右,满足加工精度要求。
..........
参考文献(略)