第一章 绪论
1.1 研究背景与意义
为了应对全球石油危机与环境污染持续恶化所带来的种种负面影响,维持汽车产业的快速稳定发展,世界各大汽车制造厂商和科研机构纷纷加大对新能源汽车技术的研发力度,以新能源汽车代替传统的燃油动力汽车,形成了多种汽车技术共同发展的局面[1]。为了缓解我国能源供给与需求之间的不平衡,保证能源安全,同时确保国内汽车产业的可持续发展,建设资源节约型、环境友好型社会,新能源汽车技术,尤其是混合动力汽车技术的发展势在必行。在各种新能源汽车中,由于混合动力汽车不需要基础设施投资,性价比远高于纯电动汽车以及燃料电池汽车,使用燃料与传统汽车相似,而且污染物排放量明显低于传统汽车,因此在各大城市公交系统的新能源汽车中使用最多[2]。相对于传统汽车与其他新能源汽车,混合动力汽车具有以下优势:(1) 混合动力汽车的发动机功率较小,燃油消耗和污染物的排放明显降低;车载发动机可为电池充电,大大提高了车辆的行驶里程。(2) 在汽车下坡、制动时,可以回收多余的动能储存在电池中,提高能量利用率。(3) 在路况良好的城市道路行驶时,可以关闭发动机,只通过电池释放能量为整车提供所需动力,可减少污染物的排放。(4) 能够利用现有设施为车辆进行加油,不需要单独建设相关基础设施。(5) 工作模式较多,发动机与电动机均可单独驱动车辆行驶,也可由发动机与电动机共同驱动车辆行驶,动力性较好。混合动力汽车各状态蓄电池与发动机配合提供动力如图 1.1 所示,车辆在良好路面行驶时,发动机停止工作,只需通过蓄电池的电力驱动电动机;车辆在加速行驶时,发动机开始工作,此时通过发电机与蓄电池双方的电力驱动电动机进行工作;车辆在制动过程中,发动机停止工作,此时电动机起着发电机的作用,利用刹车产生的能量为蓄电池充电。
..........
1.2 国内外研究现状
作为车辆各部件的装配基体,车架不仅要承载发动机、天然气瓶、车体以及乘坐人员的重量,还要承受来自车辆在行驶过程中所受到的各种力和力矩的作用[4]。因此,车架的强度不仅关系到车辆的正常使用,更与车辆的安全性密不可分。在进行车架设计时,一定要满足一定强度和刚度条件,所以在车架的设计过程中需要进行大量的强度与刚度的分析计算。传统的车架强度与刚度的分析计算主要依靠传统的经验设计方法,对复杂的车架结构做一定程度的简化处理后,进行计算分析,再对分析结果进行验证。这种传统的经验设计方法虽然简单易行,但是却对车架的结构做了大量的简化,因此会造成各部分结构的强度和刚度不合理,不能达到最终优化设计的目的,并且传统的设计方法设计周期长,从而导致产品更新速度较慢,在快速发展的现代化商品竞争市场中处于劣势。近年来,随着科学技术的不断发展,国内外开始对车架的有限元分析方法进行了大量的研究。国外在二十世纪六十年代中后期就已经开始使用有限元技术对车架进行强度与刚度的计算。到了七十年代,随着计算机技术的不断发展以及大型有限元分析软件的出现,对车架结构有限元分析正式拉开帷幕。如 Beermann[5]对某货车车架的横梁与纵梁连接部位采用梁、板混合单元离散为有限元模型,从而合理的简化分析计算。Hadad[6]等人把对车架的设计与有限元分析紧密结合,对车架进行了有限元分析,按照分析结果设计合理的实验验证方案对车架进行优化设计。Wang 等[7]使用有限元分析软件,模拟货车以不同的速度对墙壁进行碰撞,根据不同碰撞速度对货车进行静态和动态特性分析,将实际的撞击试验与有限元分析的结果进行比照,为车辆的设计研究提供了参考依据。在国内,利用有限元分析法对车辆的研究出现的比较晚。近年来随着我国科学技术的迅猛发展以及计算机技术的广泛使用,使得有限元分析法在汽车及机械领域得到快速的发展,并取得了显著的研究成果。
..........
第二章 混合动力城市客车车架结构有限元分析
作为混合动力城市客车的重要承载件,车架不仅要承受来自发动机、天然气瓶、蓄电池、车身、乘客等的重量,同时也要承受客车在行驶过程中所产生的各种力和力矩的作用。在各种路况下行驶时,还会产生作用于车架上的附加载荷。因此,车架在设计过程中必须保证具有足够的强度和刚度来承受作用在它上面的各种载荷。如果车架的强度和刚度不能满足要求,可能会造成车架疲劳损坏等各种现象,不仅会影响车辆的使用寿命,还可能对乘员的生命财产安全造成威胁。因此利用有限元分析软件 ANSYS Workbench 对车辆常见的几种典型工况进行静力学分析,得到车架的应力分布和变形情况,以便于对车架结构进行强度与刚度的校核,从而最大程度地保证车架结构的机械性能,降低生产制造成本。
2.1 有限元方法简介
二十世纪八十年代以前,对车架强度和刚度的分析主要采用传统的计算方法,即将车架简化为两根纵梁,然后采用经验公式和经典力学理论对车架的强度和刚度进行计算。该方法不仅没有考虑车架的局部变形,也没有对车架在实际工况下进行研究和分析,导致设计过程复杂,设计周期长,产品设计效率低。有限元法是数值分析方法的一种,基本思想是用一个离散的结构单元来代替原来的模型结构,从而使后续的计算分析都在这个离散的结构上进行。有限元法具有各种各样的单元集,能够适应各种结构的简化,所以有限元法可以求解任意结构复杂的问题,而且具有较高的计算精度。有限元分析的基本步骤主要包括有限元模型建立、有限元模型求解与有限元模型后处理三个阶段[26],如图 2.1 所示。(1) 有限元模型建立。为了给计算机软件提供求解的模型,其主要本质是模型的离散,主要包括几何模型的离散,单元特性的选择,定义材料属性,划分网格,检查模型与施加边界条件等。(2) 有限元模型求解。有限元法在求解之前首先要确定未知量的类型,主要求解方法有位移法、力法以及混合法,目前计算机软件中最常用的是位移法。(3) 有限元模型的后处理。由于有限元法的计算结果只是模型节点的位移和单元的数字信息,从而导致我们没有办法对这些大量的数据进行简单的综合判断,使数据处理显得非常麻烦。因此需要对求解的结果进行处理后以图像的形式来直观显示,增强可视性。
...........
2.2 混合动力城市客车整车参数
某公司最新生产的某款混合动力城市客车,采用最新的科研技术,具有节能环保、降低噪音以及驾驶舒适等特点,是城市公交用车的首选。该车采用以锂离子电池组与天然气作为混合动力源来驱动车辆的行驶。该混合动力城市客车示意图如图2.2 所示,整车参数与动力系统参数分别如表 2.1 与表 2.2 所示。作为有限元模型的基础,几何模型一般主要通过以下两种方法建立[28]:(1) 直接利用有限元分析软件建立模型。对于一些结构简单的几何模型可以利用 ANSYS Workbench 自带的几何建模模块进行模型的建立。(2) 利用三维建模软件进行实体模型的导入。对于结构复杂或者尺寸较大的模型,利用有限元软件直接建模不仅会增加建模的工作量,而且部分结构处理不够精确,如倒角、边界问题等,因此一般采用通用的三维建模软件,如 SolidWorks、Pro/E、CATIA 等建立结构的三维几何模型。利用三维建模软件与有限元分析软件 ANSYS Workbench 之间的接口,将建立好的几何模型导入到 ANSYS Workbench 中进行接下来的有限元分析,可以节省大量时间,提高工作效率。
...........
第三章 基于整车虚拟样机客车车架动态载荷有限元分析......29
3.1ADAMS/Car 软件简介..........29
3.2 混合动力城市客车整车模型建立.....32
3.3 混合动力城市客车整车虚拟样机模型仿真..........43
3.4 基于动态载荷峰值力的车架有限元分析.......47
3.5 本章小结..........48
第四章 混合动力城市客车车架结构轻量化设计........51
4.1 结构优化设计介绍........51
4.2 混合动力城市客车车架结构优化.....53
4.2.1 优化设计过程......53
4.2.2 优化设计结果求解....55
4.3 优化前后车架结构静态性能对比.....57
4.4 改进前后车架结构动态性能对比.....59
4.5 本章小结..........60
第五章 结论与展望.......63
5.1 结论....63
5.2 展望....64
第四章 混合动力城市客车车架结构轻量化设计
研究表明,车辆在行驶过程中的能量消耗与车辆自身重量成正比,车辆质量每减少 10%,可节省能量 6%~8%,对于新能源汽车来说,减少整车质量能够有效降低车辆的能源消耗并增加续航里程。车架作为混合动力城市客车的重要组成部分,其质量在混合动力城市客车整车质量中的占比较大,通过减少车架质量,不仅可以增加客车的续航里程,改善加速性能,同时可以提高客车的制动性能。
4.1 结构优化设计介绍
优化设计是指在保证产品满足一定条件的前提下,通过改变产品的一些设计变量,如尺寸、结构、形状等,使产品的各项性能达到最佳状态[66]。作为优化设计重要的三要素,设计变量是指在优化设计过程中为了提高产品的结构性能,需要进行改变的一组参数;目标函数是指设计者期望实现的产品最优性能;约束条件是指在优化设计过程中对设计变量所做的限制条件[67]。结构拓扑优化作为结构设计的概念设计阶段,是指以结构件材料的布局结构作为优化对象,通过结构拓扑优化设计,可以在材料分布均匀的设计范围内找出材料的最优分布方案;结构形状优化作为结构设计的基本设计阶段,是指在设计人员对结构形状有了一定设计思路后,以该结构件的形状作为优化对象,通过进行优化设计计算,得到结构件形状的最佳设计方案;结构尺寸优化作为结构设计的详细设计阶段,是指在不改变结构的布置形式与几何模型结构的前提下,以结构件材料的长度、厚度等设计参数作为设计变量,通过进行优化设计计算,得到结构件尺寸的最佳设计方案。传统的车架优化设计是由设计人员提供几种不同的设计方案,从中进行比较得出最优化的一种方案,该方法主要是建立在设计人员经验的基础上,但由于时间、经验的限制,可供选择的方案数量有限,不一定包含最优方案,或者不一定能够挑选出最优的设计方案,因此这种方法设计的结构往往达不到最优化的目的[70]。近年来,随着计算机技术与优化方法的不断结合与发展,在对产品进行优化的过程中,大大缩短了产品优化设计的周期,降低了成本,同时提高了产品优化的质量。
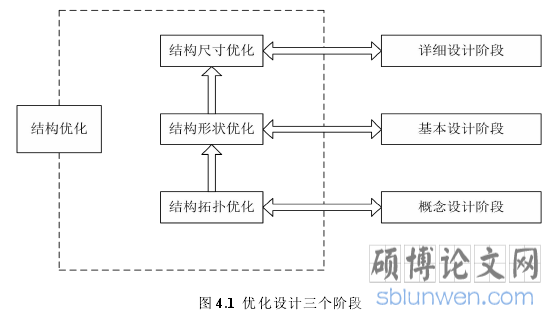
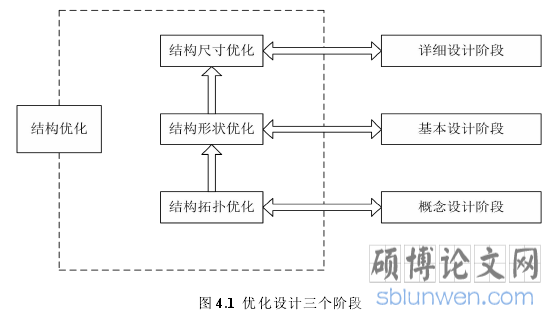
..........
结论
车架是车辆的主要承载部件,同时车架质量也占据了整车质量的很大部分。以某公司生产的某混合动力城市客车车架作为研究对象,分别对该车架进行静态载荷与动态载荷的有限元分析,并选取车辆行驶各工况中的最危险工况进行车架结构的轻量化研究。其主要研究内容及结论如下:
(1) 根据某公司提供的混合动力城市客车车架的二维图纸以及相关设计数据,利用三维软件 SolidWorks 建立车架的三维几何模型。在有限元分析软件 ANSYSWorkbench 中,选择四面体单元对车架结构进行网格划分,对划分后的网格进行质量评估。评估结果表明所划分网格质量达到标准,在此基础上对车架满载弯曲、满载扭转、满载制动、满载加速及满载转弯五种典型工况进行基于静态载荷的有限元分析。分析结果表明:在该五种典型工况下的车架最大变形量分别为 20.17mm、32.73mm、27.07mm、25.72mm、28.09mm,最大变形量均小于允许的车架各段总成最大变形量;车架的最大等效应力分别为 114.49MPa、151.90MPa、142.34MPa、137.83MPa、142.37MPa,最大等效应力均小于车架结构材料的最大极限应力,且具有一定的冗余量。其中,满载扭转工况下车架的等效应力最大,表明该工况为车架的最危险工况。通过模态分析理论,由于车架结构的低阶振动对其结构影响较大,计算车架前六阶模态,对模态结果就进行分析。结果表明:车架各阶固有频率均高于路面激振频率 3Hz;一阶固有频率为 17.78Hz,与发动机怠速频率 30Hz 相差较大,因此车架发生共振的可能性较小,不会因为共振现象影响车架安全性能。
(2) 为了使车架强度与刚度分析结果更符合实际工况,根据对混合动力城市客车整车结构分析,建立包括前后悬架模型、钢板弹簧模型、转向系统模型、前后轮胎模型、车身模型、车架模型、发动机模型、制动模型、乘客及其他附属结构模型的整车虚拟样机模型。对车架最危险工况——满载扭转工况进行动态仿真,根据仿真结果提取车架各主要载荷连接点的动态载荷峰值力,将所提取各动态载荷峰值力作为载荷条件施加到车架相应部位,进行满载扭转工况的有限元分析。分析结果表明,基于动态载荷的车架结构最大变形量为 37.77mm,最大等效应力为 225.64MPa,相比静态载荷时的最大变形量与最大等效应力,有较大的增加。
..........
参考文献(略)