第一章 绪论
1.1 选题背景与意义
制造业是衡量一个国家生产力水平的标准,也一直是我国重点发展的行业。但是随着生活水平的提升导致人工费用的增加以及人口红利的逐渐消失,传统的制造业遇上了瓶颈难以继续发展下去,为了克服难关,传统制造业结合计算机、电子信息、机械、材料等多方面的高新技术成果发展为今天的先进制造业。手机制造、汽车生产、快递分拣等多个行业对原有的人工生产线进行改造升级,投入大量资金引进最先进的自动化生产线技术,显著的提高了生产线的自动化程度,更有甚者实现了真正意义上的全自动化生产车间。随着工业 4.0 的推动,制造业迎来了巨大的创新,生产率与利润率得到了巨大增长,Mathworks 高级工程经理乔斯·马丁指出,工业发展在未来几年会呈现七大发展趋势[1]。其中自动化机器人与虚拟调试又息息相关[2]。随着生产线自动化程度的不断提升以及自动化设备的大量引入,生产线的功能结构变的越来越复杂与多功能化,对此在自动化生产线的改造时的改造难度也大大提升,对技术人员需要掌握的技能也更加复杂。电气自动化工程师需要具备多个学科的技术。例如计算机技术、通信技术还有电气仪表技术等[3]。在自动化生产线改造过程中的调试部分变的更加的复杂,尤其是在自动化程度日渐提高的今天。生产线中的每一样设备都有着很高的价值,而自动化调试的过程就是在试运行过程中发现问题并去解决问题的过程,在这些过程中一些无法预料到的问题是不可避免的,可能就因为某一个小小的失误就损坏了昂贵的设备,导致自动化生产线的改造时间增加。无论是从经济成本还是时间成本来看都是巨大的问题。如果只是单纯的增加成本这样的结果还是可以接受的,然而事实是还会对调试人员的人身安全造成威胁[4]。对此,调试技术的研究与优化就显得至关重要。
自动化生产线的调试一般有五个步骤,分别是设备检查、单点测试、功能测试、仿真联调、负载联调。每一个步骤都需要在现场才能进行,并且这五个过程必须严格按照顺序进行。一切的工作都需要在生产线装配完成的基础上才能完成,这就极大的浪费了时间成本,因为生产线的装配是整个调试过程耗时最久的一环,装配完成之后也有着各种各样的问题需要去解决。本文提出的自动化调试系统就提供了一种可能性,可以在装配生产线的同时进行一部分工作,调试系统无需实际设备与实际 PLC 控制器,本文利用虚拟的 PLC 替代实际设备来实现对生产线的模拟调试。最显著的优点就是使用自动化调试技术可以减少过程停机时间,并且可以降低将产品的设计转换成实际产品的过程风险,因为在生产过程中如果因为编程方面与软件方面出现问题将会带来高昂的代价,可能需要花费大量的金钱与时间去解决。在虚拟环境中建立生产线并进行调试另外一大优点是可以节约时间与成本,并在这种虚拟的环境下提前发现问题,甚至能够在一定程度上对未来的挑战进行预示。最后实际的生产将在可靠的生产计划下完成,并且能够缓解实际调试过程中的停机问题以及生产损失的问题。
.........................
1.2 自动化调试技术概述与研究现状
1.2.1 PLC 在自动化中的研究现状
可编程序控制器是微机控制技术和继电器控制技术相互结合的产物,它是一台基于顺序控制器的数控工业计算机。早在 20 世纪 70 年代,第一台 PLC 控制器就由美国 DEC 公司研制出来[5]。原 PLC 控制器只能用于简单的逻辑运算、计时和计数。随后的 10 年中 PLC 控制器的主要控制功能得到迅速发展,尤其是多种 8 位微处理器的先后出现使得 PLC 技术飞速发展。到了 20 世纪 80 年代末期 PLC 控制器实现了通信功能,依赖于计算机技术的高速发展,PLC 控制器在通信方面有了很大的进展,已经初步实现了分布式通信网络体系[6]。不过因为各大公司互相竞争始终没有达成一致,不同厂家生产的产品所使用的通信系统五花八门,难以实现不同种类的产品进行通信。不过这种尴尬的局面没有持续下去,很快就有公司提出了开放通信系统,标准化的通信协议使得不同的厂家生产的产品可以相互通信,后期产品的扩展也变得更加便捷[7]。此时的 PLC 控制器功能不断完善就连软件系统也实现了标准化,同时增加了高级编程语言功能。控制技术的不断完善也推动着 PLC控制器从结构与功能的方面改进[8]。
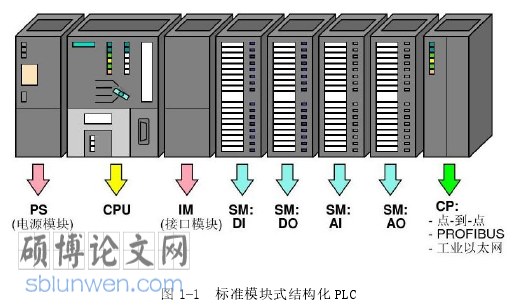
电气自动化论文怎么写
........................
第二章 调试系统需求分析与研究内容
2.1 引言
因为信息技术的发展,传统制造业面临巨大变革。在工业 4.0 的推动下,物联网、人工智能、自动化生产线、机器人等多项技术开始融合与升级。可以说这是制造行业新的机遇。 新兴的技术使得工业生产的自动化程度不断变高,给生产建设带来极大的便利,主要应用于自动化上下料、自动化检测、自动化加工等方面,在一定程度上减少了操作工人的工作量与工作时间并提高了效率[36]。因此自动化技术在今天各大行业广泛应用。与此同时自动化调试技术要求不断提高,本文设计的调试系统的目的在于减少现场调试难度。在项目初期现场设备并未齐全或装配未完成的前提下,通过 PC 机对 PLC 程序与仿真软件中的虚拟生产线进行调试,来测试和验证产品设计的合理性。实现现场设备装配与虚拟调试的同时进行,节约了调试的时间与成本,最终以最合理的方案生产,避免风险减少损失。
根据实际的功能需求分析,调试系统需要具备信号配置、通讯系统、信号交互以及数据采集等多个方面功能,同时还要具备人机交互界面简洁易操作,调试系统稳定性高、实时性强、准确率高等性能指标。本章将基于以上的需求分析和性能指标对自动化调试系统进行总体框架。
...........................
2.2 调试系统需求分析
调试系统是以计算机仿真技术为基础,结合高速发展的信息技术,模拟出现实物理环境与数字衍生系统[37]。在现场进行调试的时候,可能因为施工环境的影响、设备自身因为老旧产生的硬件问题导致机器无法正常运行以及调试人员的操作存在差异性,会导致调试过程中出现各种各样的问题。调试人员因此无法区别是程序的问题还是硬件的问题,极大的增加了调试难度和调试所需时间。然而在调试系统上进行测试时,可以有效的避免外部因素对调试过程的影响,在保证了设备、环境与人为因素的干扰之后调试过程中出现的问题都是程序引起的。在系统的调试界面对生产线进行建模,对生产线中的每一个元器件进行信号配置与交互,将 PLC程序输入后可以模拟脉冲信号发给调试系统,来控制调试界面的元器件进行逻辑动作。通过直观的二维模型的动态展示,对调试过程中出现的问题先进行直观的演示,再向调试人员解析导致该问题出现的原因和错误程序段、并指导如何处理该类问题。
系统功能需求:随着机电设备日趋科技化、大型化、复杂化,我们需要花费更多的时间对其进行调试和维护[38]。在当前大环境下自动化调试人员需要亲临现场进行调试,然而现场调试却又诸多问题,比如成本高、风险高但是效率却很低的情况。其因素又包含现场调试环境艰苦、工况复杂以及设备运行不稳定等。并且现场调试过程中大部分生产线的各项设备多采用现场总线通信方式进行通信。现场总线虽然具有简单、可靠、经济、实用等一系列优点,受到现场调试人员的广泛欢迎,但也有不容忽视的缺点。在网络通信中,数据包的传输延迟、通信系统的瞬时错误和数据包丢失、发送和到达顺序的不一致都会破坏传统控制系统的原有确定性,使控制系统的分析和综合更加复杂,并对控制系统的性能产生负面影响[39]。针对自动化生产线调试过程中难度大、工程量多、效率低等问题[40]。很多研究人员和公司以数字技术为基础设计了一些虚拟仿真软件,以自动化生产线为研究对象在虚拟仿真软件中进行虚拟调试。自动化生产线在调试过程中有很大一部分的工作中心就在于程序调试,现有的一些系统可以进行简单的调试但是却只能对应自己的开发平台,有很大的局限性。并且调试过程中的信号交互都是自己通过 PC 端的数据存储与读取来完成的,虽然实现了信号的交互,但是数据的采集存在缺陷。没有一个上手简洁的界面来整合系统的各项功能与结果。
.......................
第三章 调试模型建立 ........................ 21
3.1 引言 .................................................. 21
3.2 物理对象在计算机中的表达 ................................... 21
3.3 生产线模型行为分析 .............................................. 22
第四章 调试系统外部通信的实现 ........................ 33
4.1 引言 .................................................. 33
4.2 调试系统界面的设计 ............................................ 33
第五章 自动化上下料生产线调试 ......................... 49
5.1 引言 ............................................. 49
5.2 生产线建模 ....................................... 49
5.3 控制程序设计 ............................ 51
第五章 自动化上下料生产线调试
5.1 引言 在前面的工作中已经介绍了本文研究的自动化调试系统的具体功能以及详细的实现过程,在本章节针对实际项目中的自动化上下料生产线的一部分,采用本课题所研究的自动化调试系统对其进行调试,以此来详细介绍本文研究的调试系统的使用方法,验证该系统的可用行与可靠性,并对其进行测试与优化。在使用该系统之前还需要做以下准备工作:
(1)在 Scratch 中建立生产线模型,并编写脚本让生产线模型中的元器件具有实际元器件所具备的功能。
(2)针对特定的自动化生产线,分析其功能需求,设计 PLC 控制系统并且编写 PLC 程序。
(3)在调试系统中关联生产线模型与 PLC 信号。
(4)在调试系统的展示界面对自动化生产线进行调试。
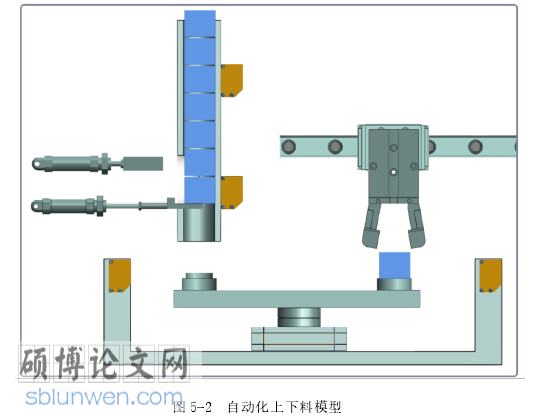
电气自动化论文参考
第六章 总结与展望
6.1 全文总结
自动化技术迅速发展带来的问题就是调试难度的增加,对此将制造技术与仿真技术结合,利用仿真技术为制造业提供有利的支持。本文主要研究了基于 Scratch软件的跨平台自动化调试技术,并且在进行了调研的基础上形成需求方案,开发了一套应用于生产线调试的系统。利用了 Scratch 的可视化功能结合编程的功能,可以实现对多平台 PLC 程序的读写并将信号传输给 Scratch 软件,可以通过消息的传输,实现对 Scratch 中模型的联动仿真,对生产线进行调试的过程。
本文的主要研究内容如下:
(1)对国内外的自动化生产线调试技术的发展历程做了分析与研究,提出研究的背景与意义。并对相关的技术进行概括,针对目前自动化调试成本高,周期长等问题提出可以在计算机上进行仿真调试的系统,分析调试系统的功能需求建立了系统的整体框架。
(2)为了可以在模型上对生产线进行调试,以 Scratch 软件为平台实现了 PLC程序控制生产线模型运动仿真,达到调试生产线的过程。为降低模型的建立难度,在 Scratch 软件中创建了常见的执行元器件的库。研究了虚拟环境下建模的一些方法以及消息驱动模型的运行机制。
(3)对 Scratch 和多种平台 PLC 的通信方法进行了研究。完成了调试系统对多平台 PLC 程序的数据采集以及数据处理。并且实现了 Scratch 软件与调试系统的通信,使得 Scratch 通过调试系统作为中转与 PLC 实现通信。根据调试系统的使用流程设计了人机交互界面。
(4)以自动化上下料生产线为实验对象,设计了自动化控制程序,与自动化生产线模型的建立,对开发的自动化调试系统的可行性进行验证,证明了调试系统的可行性。
参考文献(略)